Introduction.
The evolution of Programmable Logic Controllers (PLCs) has profoundly shaped the landscape of industrial automation. From their origins in relay logic systems to their integration with cutting-edge technologies, PLCs have been instrumental in revolutionizing how industries operate. This journey has seen significant milestones, including the birth of relay logic, the creation of the first true PLC by Dick Morley, and the adoption of industry standards. Today, PLCs continue to dominate manufacturing and extend their influence into energy management, building automation, and more. However, they face challenges in scalability, integration, and maintenance. Looking ahead, the future of PLCs holds promise, with emerging technologies like IoT, AI, and machine learning poised to enhance efficiency, sustainability, and adaptability, albeit accompanied by concerns regarding cybersecurity and workforce adaptation.
Past Innovations and Achievements.
The history of Programmable Logic Controllers (PLCs) is a story of important developments and how they’ve changed the way we make things. PLCs have been a big deal in the world of automation, making factories and other processes work better and faster.
Milestones in PLC Technology.
Milestones are important moments in the history of PLC technology when it made significant advancements, allowing for more automation. These key points in the evolution of PLCs include:
1. Birth of Relay Logic:
PLCs started from relay logic, an old way of controlling machines using switches and wires. This old method from the early 1900s was the starting point for developing PLCs.
2. Introduction of the Modicon 084:
In 1968, a big step forward happened with the creation of the Modicon 084 made by Dick Morley. This device is seen as the first real PLC and it changed the way control systems worked, shifting from relying on physical parts to using computer programs to control things.
3. Evolution of the PLC-3 and PLC-5:
In the 1970s and 1980s, Allen-Bradley created the PLC-3 and PLC-5. These machines were better because they could do multiple tasks at once and store more information which made industries work better.
4. Adoption of the IEC 61131 Standard:
The IEC 61131 standard made it easier for engineers to talk to PLCs by creating common languages like ladder logic and function block diagrams. This helped make things more consistent and compatible in the industry.
Early Origins and Development
To truly understand how PLC technology came to be it’s important to know about its early stages which can be broken down into these phases:
1. Emergence of Relay-Based Control Systems:
Before PLCs were invented industries used relay-based systems to control machines and processes. These systems worked but had limitations because they couldn’t easily adapt or grow.
2. Dick Morley and the “Father of the PLC”:
Dick Morley, an American engineer is known as the “Father of the PLC.” He became famous for inventing the Modicon 084 a device that replaced complicated relay systems. This all started with a bet made during a casual drink with friends. The bet was to create a controller that could do the job of those complex relays. And Morley succeeded changing the way industrial automation works.
3. Transition to Digital Logic:
PLC technology changed how we control things. It went from using older less advanced methods to using computers with memory. This made it easier for engineers to make and change control programs.
Advancements in Programmable Logic Controllers
As technology got better, PLCs also improved a lot. Some important changes were made to make them more powerful and useful. These changes include:
1. Microprocessor Integration:
Adding tiny but powerful chips to PLCs made them much better. They can now follow instructions and do difficult math stuff much faster.
2. Enhanced Communication Protocols:
PLCs have changed to work better with modern technology. They can now talk to other machines using things like Ethernet/IP, Profibus and Modbus TCP/IP. This makes it easier to share information and check on things from far away.
3. Scalability and Modularity:
Modern PLCs can be adjusted and changed to fit the needs of different industries like car factories or food processing.
Real-World Applications
The real value of any new technology is seen in how it’s used in the real world. PLCs are now being used in many different situations changing how industries work.
1. Manufacturing and Assembly Lines:
PLCs are like secret champions in factories. They manage tricky tasks like putting things together just right and making sure everything moves smoothly. They’re in charge of robots and conveyor belts making sure everything is made perfectly.
2. Building Automation:
In building automation PLCs control things like heating, cooling, lights and security making buildings use less energy and safer.
3. Energy Management:
PLCs are important for managing energy, controlling how power is sent around, keeping an eye on how much energy is used and making smart grids work better.
4. Water Treatment and Wastewater Management:
Water treatment plants use special computer systems to make sure our drinking water is clean and safe. These systems also help manage dirty water to keep our environment clean.
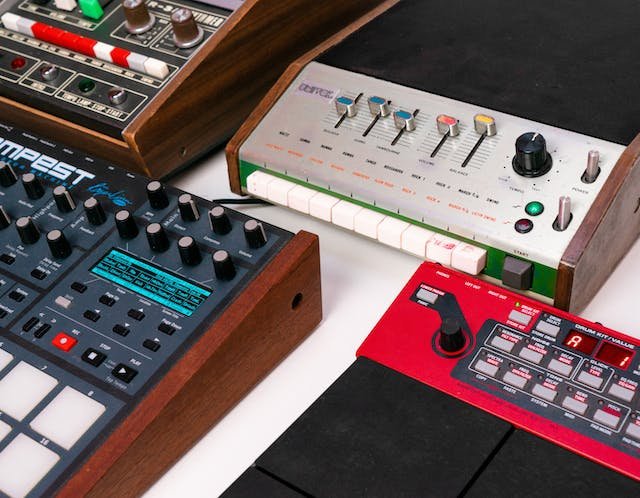
Current Landscape of PLC in Industrial Automation
In today’s world of advanced automation Programmable Logic Controllers (PLCs) play a crucial role in coordinating and controlling various tasks in different industries. These devices are particularly important in manufacturing. They make things run smoothly, but there are some issues like expanding the system and keeping it in good shape. Let’s take a closer look at what’s happening in this field and the challenges it faces.
The Dominance of PLC in Manufacturing
PLCs are vital in manufacturing. They work seamlessly on assembly lines and production floors, making things run efficiently. They control various tasks from robots to conveyor belts to ensuring everything works smoothly.
In the world of automation PLCs give manufacturers an advantage as they can control things in real-time and adjust to changing needs with accuracy. As manufacturing changes, the PLCs are still essential for keeping quality high, improving production and reducing mistakes.
Key Industries Utilizing PLC
PLCs are not just for factories other important industries use them too. These industries are:
1. Energy and Utilities:
PLCs are like energy superheroes in the power world. They help control where electricity goes, keep an eye on how much is used and make sure smart grids work smoothly. They’re like the protectors of energy efficiency.
2. Building Automation:
In smart buildings, PLCs are like the brain that controls things to make the place comfy and safe. They manage the temperature, air, lights and security.
3. Food and Beverage:
In cooking and making drinks, PLCs make sure everything is done just right. They help keep the taste and safety the same every time from following recipes to checking the quality of what’s made.
4. Water Treatment and Wastewater Management:
Water treatment and cleaning our used water wouldn’t work well without PLCs. They are like silent helpers that make sure our water is safe and stays around for a long time.
Challenges Faced by Traditional PLC Systems
PLCs are known for making things work automatically and efficiently but old systems face problems in today’s fast-changing technology world.
1. Scalability:
Older PLCs can struggle to adapt to the changing needs of today’s industries. Making them bigger or changing them to handle more work can be really hard.
2. Integration Issues:
As industries rely more on data and connect different machines making them talk to each other can be tricky. Making sure that computers (PLCs) can talk to all kinds of equipment needs careful planning and doing things carefully.
3. Maintenance and Downtime Concerns:
PLCs like complex machines those needed to be taken care of. But when we stop them for maintenance it can slow down work and make things less efficient. Hence, industries have to find a balance between keeping the system healthy and not causing too much disruption.
The Future of PLC in Industrial Automation
Industrial automation is changing, and the key to this change is the Programmable Logic Controller (PLC). In the future, PLCs will adapt to new technologies and global trends making it an exciting journey to see how they’ll be used in industrial automation.
Emerging Technologies and Trends
In today’s fast-paced digital era industrial automation systems are adopting new technologies and trends that will change how things work. Some important trends include:
1. Integration with IoT and Industry 4.0:
When industrial machines (PLCs) join forces with the Internet of Things (IoT) and Industry 4.0. It lets them share information instantly watch them from afar and predict when they need repairs. As PLCs get more connected industries can take charge of their operations like never before.
2. AI and Machine Learning in PLC:
Combining AI and Machine Learning with PLCs is like giving them a smart brain. These smart PLCs can adjust to changing situations, make processes work better and figure out when they need fixing. This teamwork between PLCs and AI is making automation even smarter and more advanced.
Potential Benefits and Transformations
In the future, PLCs (Programmable Logic Controllers) will bring lots of good changes to different industries. This will help them in many ways.
1. Enhanced Efficiency and Productivity:
Advanced algorithms and predictive analytics in PLCs will make operations better, reduce downtime, and help us work faster. These PLCs can make quick decisions and adjust to changes, which will make things work really well.
2. Sustainability and Green Automation:
As the world focuses more on being eco-friendly, Programmable Logic Controllers (PLCs) will be really important in making machines and systems more environmentally friendly. They’ll use smart and efficient methods to save energy, control power usage and cut down on waste. This way the industrial automation will be in harmony with taking care of the environment.
Addressing Challenges
As PLCs get better, they need to deal with problems that come with new tech and ideas. Some of these problems are:
1. Cybersecurity and Data Protection:
As we become more connected, the risk of cyberattacks goes up. It’s crucial to protect important industrial systems and data. To do that, we need strong cybersecurity and data protection rules for the future.
2. Training and Workforce Adaptation:
As technology gets better, people who work with machines need to learn new things. They will need training and education to learn how to use the new technology in machines called PLCs.
In conclusion
Programmable Logic Controllers (PLCs) have come a long way, revolutionizing industrial automation through significant milestones, from relay logic to advanced digital systems. They continue to dominate manufacturing and find applications in various industries, ensuring efficiency and reliability. However, they face challenges like scalability, integration issues, and maintenance concerns. The future of PLCs lies in their adaptation to emerging technologies such as IoT, AI, and Industry 4.0, promising enhanced efficiency and sustainability. Addressing cybersecurity and workforce adaptation will be crucial in this evolving landscape. PLCs are poised to play a pivotal role in the ever-changing world of industrial automation.